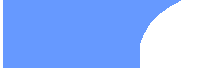         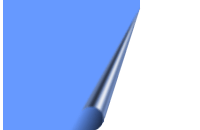 |
Controllers
1. Robot controller
The Adept SmartController™ CX is a high-performance robot and vision controller based upon Adept SmartServo architecture. Its distributed processing architecture improves performance by freeing up 30% of the processor’s resources. The Adept SmartController CX features a faster processor and conveyor belt tracking support, and optional vision guidance support. It also features several high-speed communication interfaces, including Fast Ethernet and SmartServo™. A single SmartController™ CX can control up to 2 robots through the SmartServo communication ports.
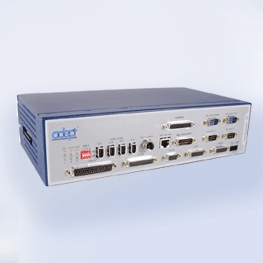
ADEPT Smart Controller CX
Technical data
Processor |
Motorola 68060 |
Memory (RAM) |
32MB |
Communication Ports |
Ethernet 10/100 BaseT (1) |
|
DeviceNet (1) |
|
RS232 (3) |
|
RS422/485 (1) |
|
SmartServo (2) |
|
IEEE 1394 (2) |
|
Belt Encoder Port |
Clock Speed |
50 MHz |
Mass Storage |
128 MB (Compact Flash) |
Expansion Slots |
NA |
Digital I/O |
12 optically isolated inputs (4 fast) |
|
8 optically isolated outputs |
|
(expansion is available) |
2. Conveyor controller
The IndraLogic L40 PLC solution is based on the innovative IndraControl L40 embedded terminal control. A number of communication interfaces simplify the integration with various control structures. Expansion with function modules enables flexible adaptation to requirements for various applications and processes. The I/O periphery is easily expandable by direct connection of Rexroth Inline modules. User-friendly and programmable using IndraWorks engineering software that is IEC 61131-3 compliant. Diagnostics are easily performed using IndraWorks or locally using the control’s integrated display.
This controller is used to command the conveyor and to gather and process data received from the identification devices through the PROFIBUS interface. It features 128 I/O ports for externat conections.
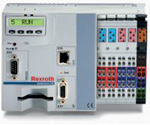
IndraControl L40
Technical data
User Memory(Code/Data) |
8 MB (4MB/4MB) |
NVRAM |
64 kB |
Number of Tasks |
16 |
Task Types |
cyclic, periodic, free running, externally event-controlled |
Processing Time |
typical, 70 µs (1000 commands in IL, bit and word commands) |
I/O |
512 I/O (central), expansion via Profibus DP (max. 126 units, per 8 kB I/O), 8 I / 8 O on board |
Programming Software |
Rexroth IndraWorks |
Programming Languages(IEC 61131-3) |
IL, LD, FBD, ST, SFC |
Programming Interface |
Ethernet, RS232 |
Functionality for Program Testing |
breakpoint, single-step, single cycle, write/force, monitoring, sampling trace, simulation, online change |
Included Libraries |
PLCopen, Communication, Standard IEC 61131-3 |
Communication Interfaces |
RS232, Ethernet, PROFIBUS-DP |
3. CNC controller
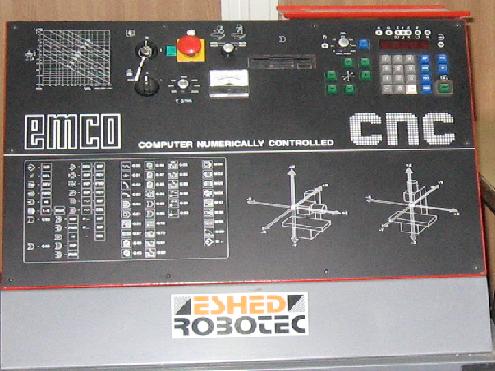
CNC machine controller user interface
Control elements for manual operation:
- Main switch
- Control lamp main switch.When the main switch is on, the lamp is on.
- Emergency stop button.Control unit, feed motors, and main motor are cut off from power by pressing emergency stop button. Main switch has to be switched on again.
- Switch for main spindle
- Turning knob for speed control of main spindle.
- Ammeter.Shows power consumption of main spindle motor.
- Feed keys for longitudinal, cross and vertical slide.
- Rapid traverse key.
- Turning knob for setting the feed rate.
- Inch/metric switch and switch for changing the axis system.
- Digital read-out for slide movement.
- Control lamp for hand operation.
- H/C switch key: hand operation/CNC operation.
- DEL key. The X, Y, Z values are set to zero.
- The → key. With the → key, u can switch from X to Y to Z without movement of the slides.
- The INP key. With the INP key you enter the values for slide movements.
- M-key. Activates switching exits.
4. Cell server
The IBM System x3500 delivers unprecedented performance and reliability for demanding distributed environments that rely on 24x7 availability of mission-critical applications. With up to eight-core processor performance at lower power consumption per core, the x3500 offers leading-edge capacity and high-speed I/O scalability. A long-life platform with 24-month availability, the x3500 minimizes deployment and support concerns.
With the x3500 take advantage of virtualization. Deploy an infrastructure with less hardware that supports the same—or more—applications with lower hardware support costs.
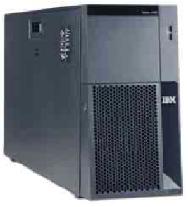
IBM X Series 3500
Technical data
Processor |
Dual-Core Intel Xeon Processor 5160, 3.0 GHz and 1333 MHz front-side bus |
Number of processors |
2 |
L2 cache |
2x2MB (dual-core) |
Memory1 |
7GB Fully Buffered DIMM 667 MHz via 12 DIMM slots |
Expansion slots |
3 PCI-Express, 2 PCI-X and 1 PCI |
Disk bays |
8 |
Maximum internal storage |
2.4TB hot-swap SAS, 4TB hot-swap SATA |
Network interface |
Integrated dual Gigabit Ethernet |
Power supply |
835W 2 |
Hot-swap components |
Power supply, fans and hard disk drives |
RAID support |
Integrated RAID-0, -1, -1E, -5, -6, -10 |
Systems management |
Automatic Server Restart; IBM Predictive Failure Analysis on hard disk drives, processors, VRMs, fans and memory; light path diagnostics with side viewable panel; integrated IPMI System Management Processor; IBM Director; optional Remote Supervisor Adapter II SlimLine and IBM ServerGuide |
Operating systems supported |
Microsoft Windows Server 2003, Windows 2000/Advanced Server, Red Hat Linux, SUSE Linux, Novell NetWare, VMware ESX Server, SCO OpenServer, SCO UNIXware |
Limited warranty |
3-year onsite limited warranty |
5. LAN communication
The proposed model includes 3 layers: Data Acquisition and Control, Communication, and Aggregate Applications.The communication layer is implemented via a 4-fold fault-tolerant communication network composed of:
- an Ethernet network connecting, through a switch, the robot controllers, the PLC , the CNC controller, the workstations and the cell server;
- a network which interconects the controllers through the digital I/O;
- a network which interconects the controllers through serial connections(RS232);
- a network which connects the workstations directly to the robot controllers through a serial connection.
Last updated 29.05.2008
 |