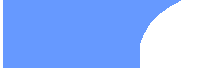         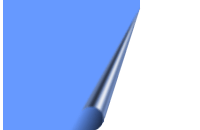 |
Objectives
The objective of the proposed project is the design, implementing, testing and validation of a holonic, fault-tolerant manufacturing control platform integrating multiple robots with visual guidance for on demand material conditioning and automated visual inspection.
The fundamental and applied research activities proposed in the project will contribute at a great extent to the development of new control architectures in the field of advanced, on demand control of flexible manufacturing structures, using multiple robotic systems. The original approach for holonic control architecture is one major contribution which, by validation and future development, represents an optimal solution for high-performance, agile behaviour of the material-handling systems – part of nowadays modern, competitive production structures.
A second original approach proposed in this project is the extension of traditional material-handling control to material-conditioning functions, allowing thus the relaxation of material flow and process constraints imposed to the transportation means, as well as on line integration of quality control in the global manufacturing system. This functional extension becomes possible in the proposed robot-vision architecture by taking over: (i) the powerful description of material flows through an efficient set of form-, surface-, and pose features of circulating parts, based on real-time, high-speed image processing and (ii) applying Artificial Intelligence concepts to reach a global autonomous, self-learning, task- and context-dependent behaviour of the robotized manufacturing system with adaptation to the working environment.
The solutions based on intelligent image processing, which are proposed in the present project, provide a unique combination that simultaneously offers a maximum of performance and efficiency, by a new approach of manufacturing automation called Rapid Deployment Automation (RDA), which considers the design of Robot Vision (RV) or Automated Visual Inspection (AVI) systems as modular development processes. Instead of dedicating strongly personalized systems to complex measuring, inspection or guidance tasks, each RDA component - camera, vision processor, robot manipulator, controller, conveyor, and even utility, development and debug software - are conceived as standard parts perfectly adaptable to the puzzle of any flexible manufacturing task. In this approach, the need of redesign and start again the construction of a complete system which must respond to new functionalities is eliminated; it suffices to remove, add, or update individual RDA components according to the current requirements.
Last but not least significant from the scientific point of view, Object Orientation is used to derive the models and information counterparts of the holonic control entities, thus providing a generic framework for adapting the designed control mechanisms to any type of material-handling agents in any flexible manufacturing structure.
The present project develops both fundamental and applied research activities in the area of controlling multi-robotic systems as material-conditioning devices in flexible production structures, according to the principles of the holonic manufacturing concept. The control architecture provides on-line adaptation of the robots to the working environment, material flow and task specifications by applying Object-Oriented and AI techniques to machine vision equipping the robot controllers.
The proposed holonic control architecture is formed by the following types of entities: Order Holons, Resource Holons, Global Scheduler, and a System Monitoring and Database entity, materialized by means of a 3-layer computing & control structure, and interconnected by means of a 4-fold fault-tolerant communication network which keeps track of the execution of production jobs.
In essence, the area of fundamental and applied research proposed in the framework of this project will contribute to the development of a high-performance infrastructure and concentration of a critical mass of highly-skilled human resources (MSc, PhD, PostDoc researchers), in national partnership, for the strategic ICT domain of European technological platform: Future in European Manufacturing – Manufuture.
The following issues are foreseen, deriving from the objectives proposed above:
- Process and system analysis, leading to the design and configuring of a generic manufacturing cell platform with four robot-vision stations, multiple stationary and mobile matrix cameras covering various fields of view including conveyor belt windows; the backbone of the manufacturing is a double-path, closed loop conveyor accessed by the robots. The layout of the cell resources will allow running different production scenarios under holonic control at batch level.
- Design and implementing of a fault-tolerant communication system between station controllers and computers (robot systems, conveyor control) and the central cell server, both at controller level and computer level.
- Methodology, control solution and algorithms for the material-conditioning problem in multi-agent production structures, applying the holonic manufacturing concept. There will be designed the layered holonic control architecture (Global Scheduler, Order Holon layer, Material-Conditioning layer, System Monitoring and Database) and implemented in a parallel processing, multi tasking software architecture.
- Design and implementing the Robot – Vision cooperation mechanisms for merged tasks: Guidance Vision of Robots (GVR) and Automated Visual Inspection (AVI) of materials. The solution is based on: (i) the description of material flows by means of sets of specific features extracted from images; (ii) configuring the operating parameters of the vision environment by virtual cameras; (iii) scene-, robot-, object-, and gripper's fingerprint modelling; (iv) the utilization of a powerful set of vision tools allowing user definable measurements and evaluation of parts.
Last updated 29.05.2008
 |